Japan is known worldwide for its quality products and services. One of the many reasons for this is its excellent quality management. How did it become so? Japan has Dr. Kaoru Ishikawa to thank for that.
Postwar Japan underwent a major quality revolution. Companies were focused on training their employees in statistical quality control. But soon they realized that the complexity of the subject itself could intimidate most of the workers; so they wanted more basic tools.
Dr. Kaoru Ishikawa, a member of the Japanese Union of Scientists and Engineers (JUSE), took it to his hands to make quality control easier for everyone – even those with little knowledge of statistics – to understand. He introduced the 7 basic tools of quality. They were soon adopted by most companies and became the foundation of Japan’s astonishing industrial resurgence after World War 2.
This post will describe the 7 basic quality tools, how to use them and give you access to templates that you can use right away.
- Quality Tools: What Are They?
- How Can Teams and Organizations Use the 7 Basic Quality Tools?
- 7 Basic Quality Tools Explained with Templates
Quality Tools: What Are They?
The 7 basic tools of quality, sometimes also referred to as 7 QC tools – represent a fixed set of graphical tools used for troubleshooting issues that are related to quality.
They are called basic quality tools because they can be easily learned by anyone even without any formal training in statistics. Dr. Kaoru Ishikawa played the leading role in the development and advocacy of using the 7 quality tools in organizations for problem-solving and process improvement.
The 7 basic quality tools include;
- Flowchart
- Histogram
- Cause-and-effect diagram
- Scatter diagram
- Check sheet
- Control chart
- Pareto chart
The 7 quality tools were first emphasized by Kaoru Ishikawa a professor of engineering at the University of Tokyo, who is also known as the father of “Quality Circles” for the role he played in launching Japan’s quality movement in the 1960s. During this time, companies were focused on training their employees in statistical quality control realized that the complexity of the subject could intimidate most of the workers; hence they opted for simpler methods that are easy to learn and use. 7 basic tools of quality were thus incorporated company-wide.
How Can Teams and Organizations Use the 7 Basic Quality Tools?
Quality tools are used to collect data, analyze data, identify root causes, and measure results in problem-solving and process improvement. The use of these tools helps people involved easily generate new ideas, solve problems, and do proper planning.
- Structured approach: They provide a systematic approach to problem-solving and process improvement, ensuring that efforts are well-organized and focused.
- Data-driven decision making: The tools enable data collection, analysis, and visualization, empowering teams to make informed decisions based on evidence.
- Improved communication and collaboration: Visual representations and structured tools facilitate effective communication and collaboration among team members, leading to shared understanding and alignment.
- Problem identification and prioritization: The tools help identify and prioritize problems or improvement opportunities, enabling teams to allocate resources efficiently and address critical issues first.
- Continuous improvement: By using these tools, teams can establish a culture of continuous improvement, as they provide a framework for ongoing monitoring, analysis, and refinement of processes.
7 Basic Quality Tools Explained with Templates
The 7 quality tools can be applied across any industry. They help teams and individuals analyze and interpret the data they gather and derive maximum information from it.
Flowchart
Flowcharts are perhaps the most popular out of the 7 quality tools. This tool is used to visualize the sequence of steps in a process, event, workflow, system, etc. In addition to showing the process as a whole, a flowchart also highlights the relationship between steps and the process boundaries (start and end).
Flowcharts use a standard set of symbols, and it’s important to standardize the use of these symbols so anyone can understand and use them easily. Here’s a roundup of all the key flowchart symbols.
Uses
- To build a common understanding of a process.
- To analyze processes and discover areas of issues, inefficiencies, blockers, etc.
- To standardize processes by leading everyone to follow the same steps.
Real-world examples of usage
- Documenting and analyzing the steps involved in a customer order fulfillment process.
- Mapping out the workflow of a software development lifecycle.
- Visualizing the process flow of patient admissions in a hospital.
Benefit
Enhances process understanding, highlights bottlenecks or inefficiencies, and supports process optimization and standardization efforts.
How to use a flowchart
- Gather a team of employees involved in carrying out the process for analyzing it.
- List down the steps involved in the process from its start to end.
- If you are using an online tool like Creately, you can first write down the process steps and rearrange them later on the canvas as you identify the flow.
- Identify the sequence of steps; when representing the flow with your flowchart, show it from left to write or from top to bottom.
- Connect the shapes with arrows to indicate the flow.
Who can use it?
- Process improvement teams mapping and documenting existing processes for analysis.
- Business analysts or consultants analyzing workflow and process optimization opportunities.
- Software developers or system designers documenting the flow of information or interactions in a system.
To learn more about flowcharts, refer to our Ultimate Flowchart Tutorial.
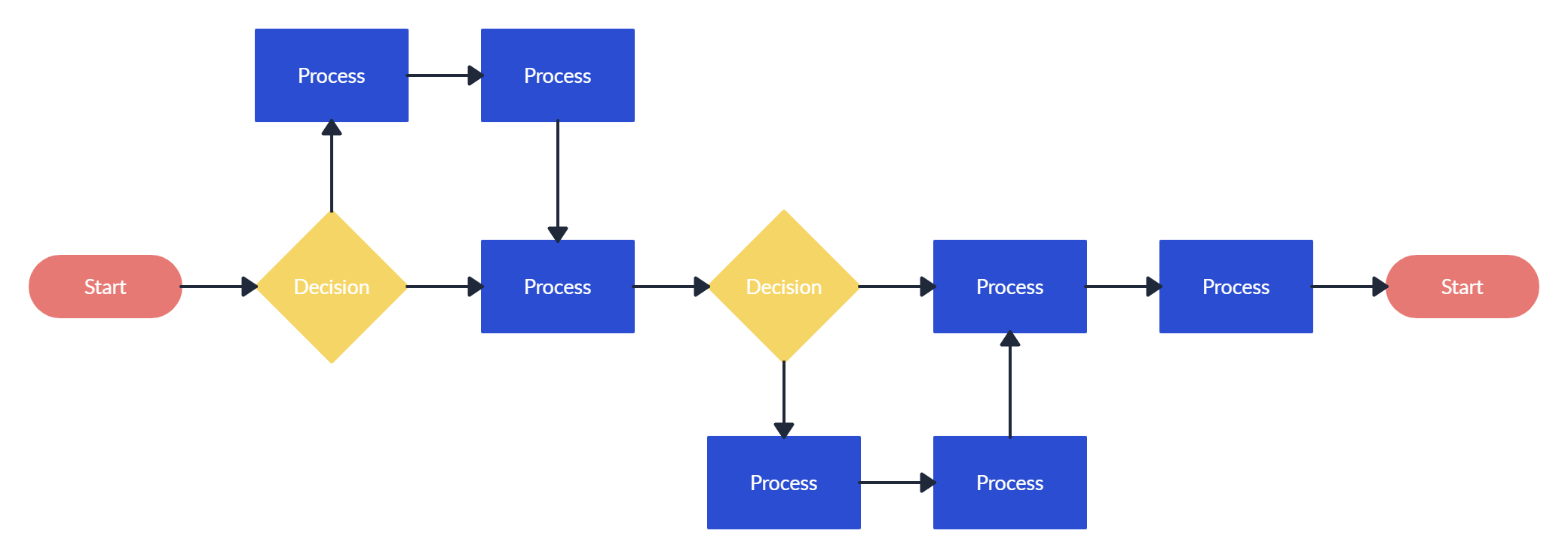
Histogram
A histogram is a type of bar chart that visualizes the distribution of numerical data. It groups numbers into ranges and the height of the bar indicates how many fall into each range.
It’s a powerful quality planning and control tool that helps you understand preventive and corrective actions.
Uses
- To easily interpret a large amount of data and identify patterns.
- To make predictions of process performance.
- To identify the different causes of a quality problem.
Real-world examples of usage
- Analyzing the distribution of call wait times in a call center.
- Assessing the distribution of product weights in a manufacturing process.
- Examining the variation in delivery times for an e-commerce business.
Benefit
Provides insights into process performance and variation, enabling teams to target areas for improvement and make data-driven decisions.
How to make a histogram
- Collect data for analysis. Record occurrences of specific ranges using a tally chart.
- Analyze the data at hand and split the data into intervals or bins.
- Count how many values fall into each bin.
- On the graph, indicate the frequency of occurrences for each bin with the area (height) of the bar.
Who can use it?
- Process engineers or data analysts examining process performance metrics.
- Financial analysts analyzing expenditure patterns or budget variances.
- Supply chain managers assessing supplier performance or delivery times.
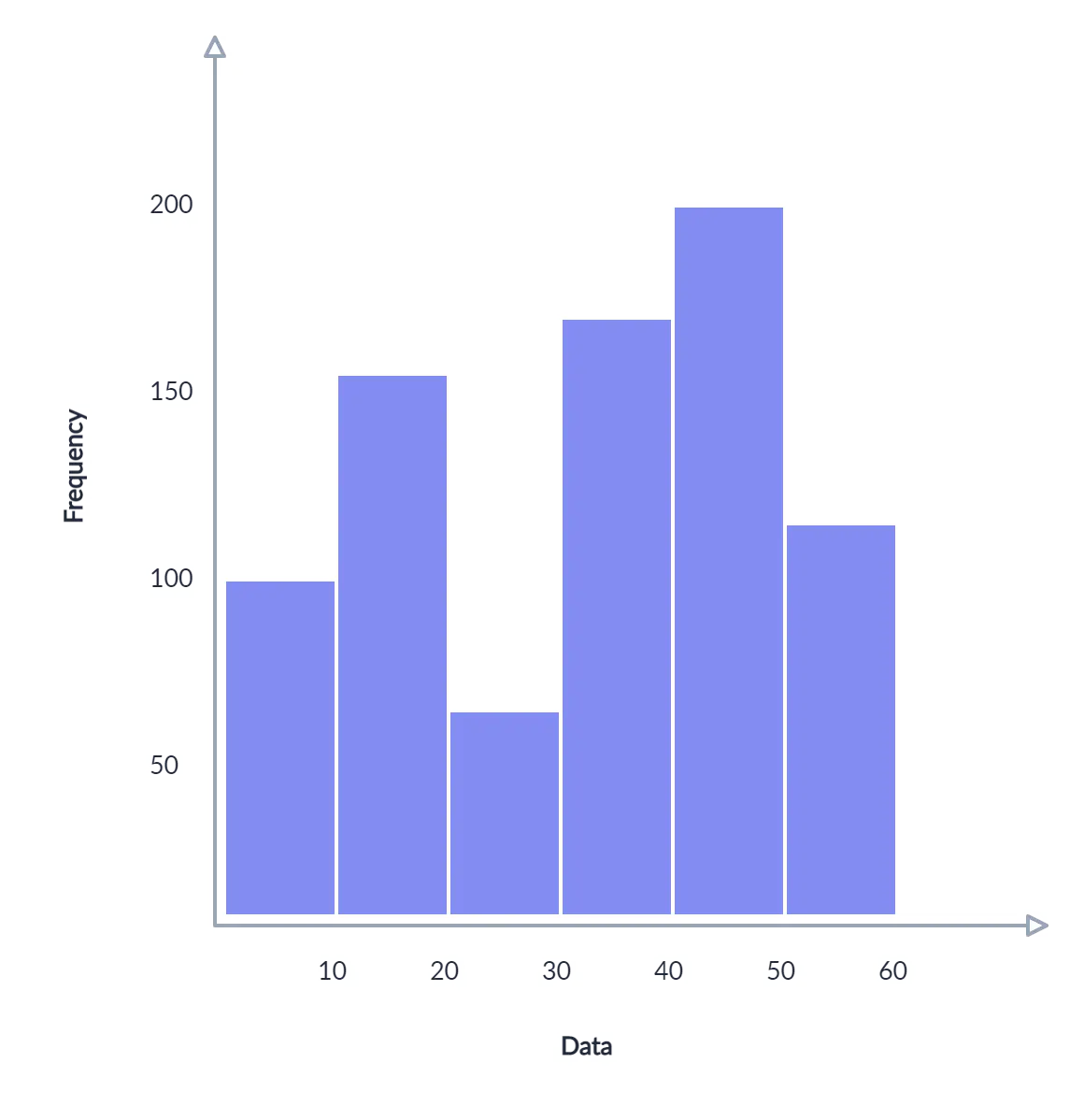
Here’s a useful article to learn more about using a histogram for quality improvement in more detail.
Cause and Effect Diagram
This tool is devised by Kaoru Ishikawa himself and is also known as the fishbone diagram (for it’s shaped like the skeleton of a fish) and Ishikawa diagram.
They are used for identifying the various factors (causes) leading to an issue (effect). It ultimately helps discover the root cause of the problem allowing you to find the correct solution effectively.
Uses
- Problem-solving; finding root causes of a problem.
- Uncovering the relationships between different causes leading to a problem.
- During group brainstorming sessions to gather different perspectives on the matter.
Real-world examples of usage
- Investigating the potential causes of low employee morale or high turnover rates.
- Analyzing the factors contributing to product defects in a manufacturing process.
- Identifying the root causes of customer complaints in a service industry.
Benefit
Enhances problem-solving by systematically identifying and organizing possible causes, allowing teams to address root causes rather than symptoms.
How to use the cause and effect diagram
- Identify the problem area that needs to be analyzed and write it down at the head of the diagram.
- Identify the main causes of the problem. These are the labels for the main branches of the fishbone diagram. These main categories can include methods, material, machinery, people, policies, procedures, etc.
- Identify plausible sub-causes of the main causes and attach them as sub-branches to the main branches.
- Referring to the diagram you have created, do a deeper investigation of the major and minor causes.
- Once you have identified the root cause, create an action plan outlining your strategy to overcome the problem.
Who can use it?
- Cross-functional improvement teams working on complex problems or process improvement projects.
- Quality engineers investigating the root causes of quality issues.
- Product designers or engineers seeking to understand the factors affecting product performance.
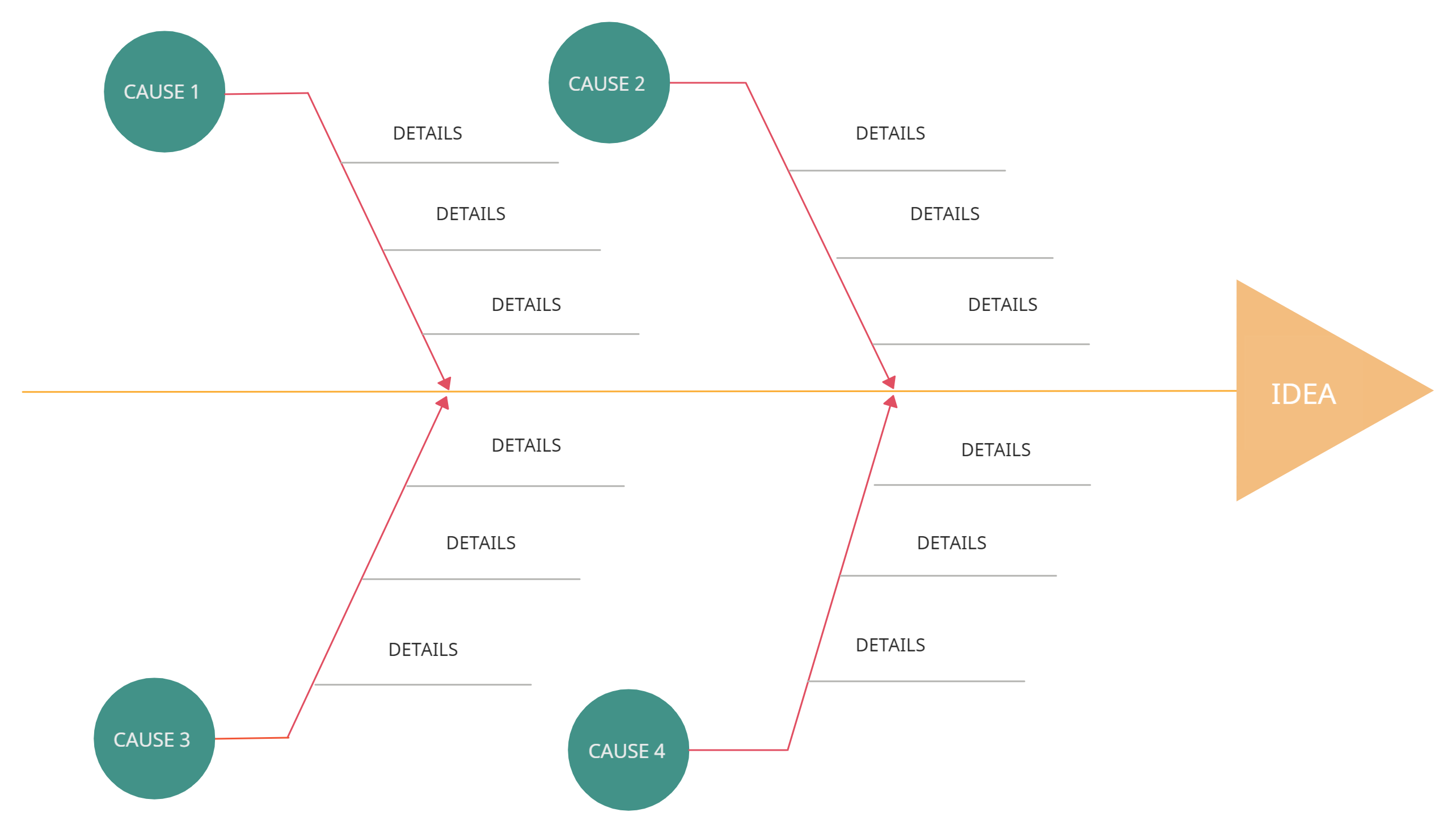
Scatter Diagram
The scatter diagram (scatter charts, scatter plots, scattergrams, scatter graphs) is a chart that helps you identify how two variables are related.
The scatter diagram shows the values of the two variables plotted along the two axes of the graph. The pattern of the resulting points will reveal the correlation.
Uses
- To validate the relationship between causes and effects.
- To understand the causes of poor performance.
- To understand the influence of the independent variable over the dependent variable.
Real-world examples of usage
- Exploring the relationship between advertising expenditure and sales revenue.
- Analyzing the correlation between employee training hours and performance metrics.
- Investigating the connection between temperature and product quality in a production line.
Benefit
Helps identify correlations or patterns between variables, facilitating the understanding of cause-and-effect relationships and aiding in decision-making.
How to make a scatter diagram
- Start with collecting data needed for validation. Understand the cause and effect relationship between the two variables.
- Identify dependent and independent variables. The dependent variable plotted along the vertical axis is called the measures parameter. The independent variable plotted along the horizontal axis is called the control parameter.
- Draw the graph based on the collected data. Add horizontal axis and vertical axis name and draw the trend line.
- Based on the trend line, analyze the diagram to understand the correlation which can be categorized as Strong, Moderate and No Relation.
Who can use it?
- Data analysts exploring relationships between variables in research or analytics projects.
- Manufacturing engineers investigating the correlation between process parameters and product quality.
- Sales or marketing teams analyzing the relationship between marketing efforts and sales performance.
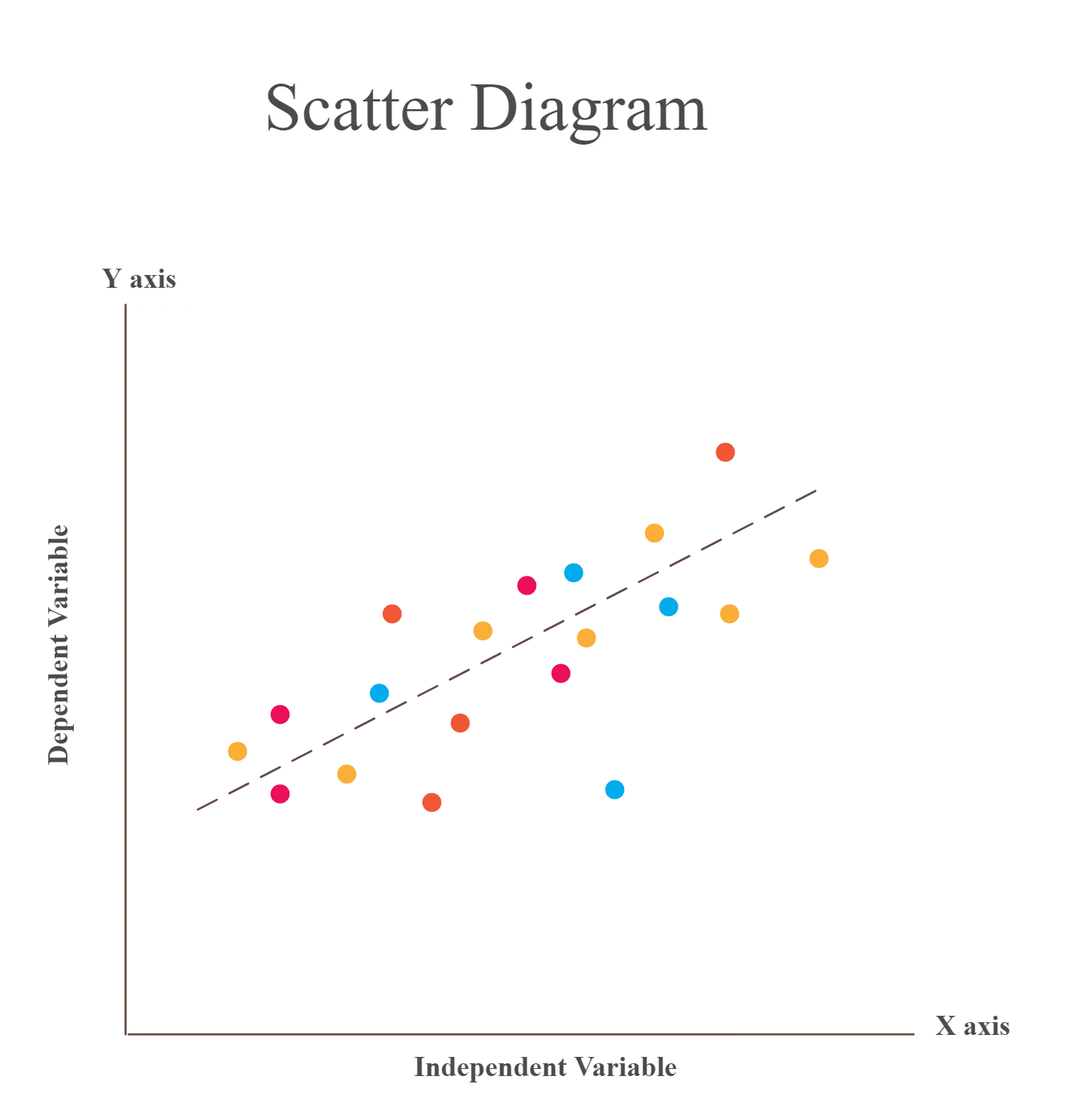
Check Sheets
Check sheets provide a systematic way to collect, record and present quantitative and qualitative data about quality problems. A check sheet used to collect quantitative data is known as a tally sheet.
It is one of the most popular QC tools and it makes data gathering much simpler.
Uses
- To check the shape of the probability distribution of a process
- To quantify defects by type, by location or by cause
- To keep track of the completion of steps in a multistep procedure (as a checklist)
Real-world examples of usage
- Tracking the number of defects or errors in a manufacturing process.
- Recording customer complaints or inquiries to identify common issues.
- Monitoring the frequency of equipment breakdowns or maintenance needs.
Benefit
Provides a structured approach for data collection, making it easier to identify trends, patterns, and areas for improvement.
How to make a checksheet
- Identify the needed information.
- Why do you need to collect the data?
- What type of information should you collect?
- Where should you collect the data from?
- Who should collect the data?
- When should you collect the data?
- How should you measure the data?
- How much data is essential?
Construct your sheet based on the title, source information and content information (refer to the example below).
Test the sheets. Make sure that all the rows and columns in it are required and relevant and that the sheet is easy to refer to and use. Test it with other collectors and make adjustments based on feedback.
Who can use it?
- Quality inspectors or auditors who need to collect data on defects or issues.
- Process operators or technicians responsible for tracking process parameters or measurements.
- Customer service representatives who record customer complaints or inquiries.
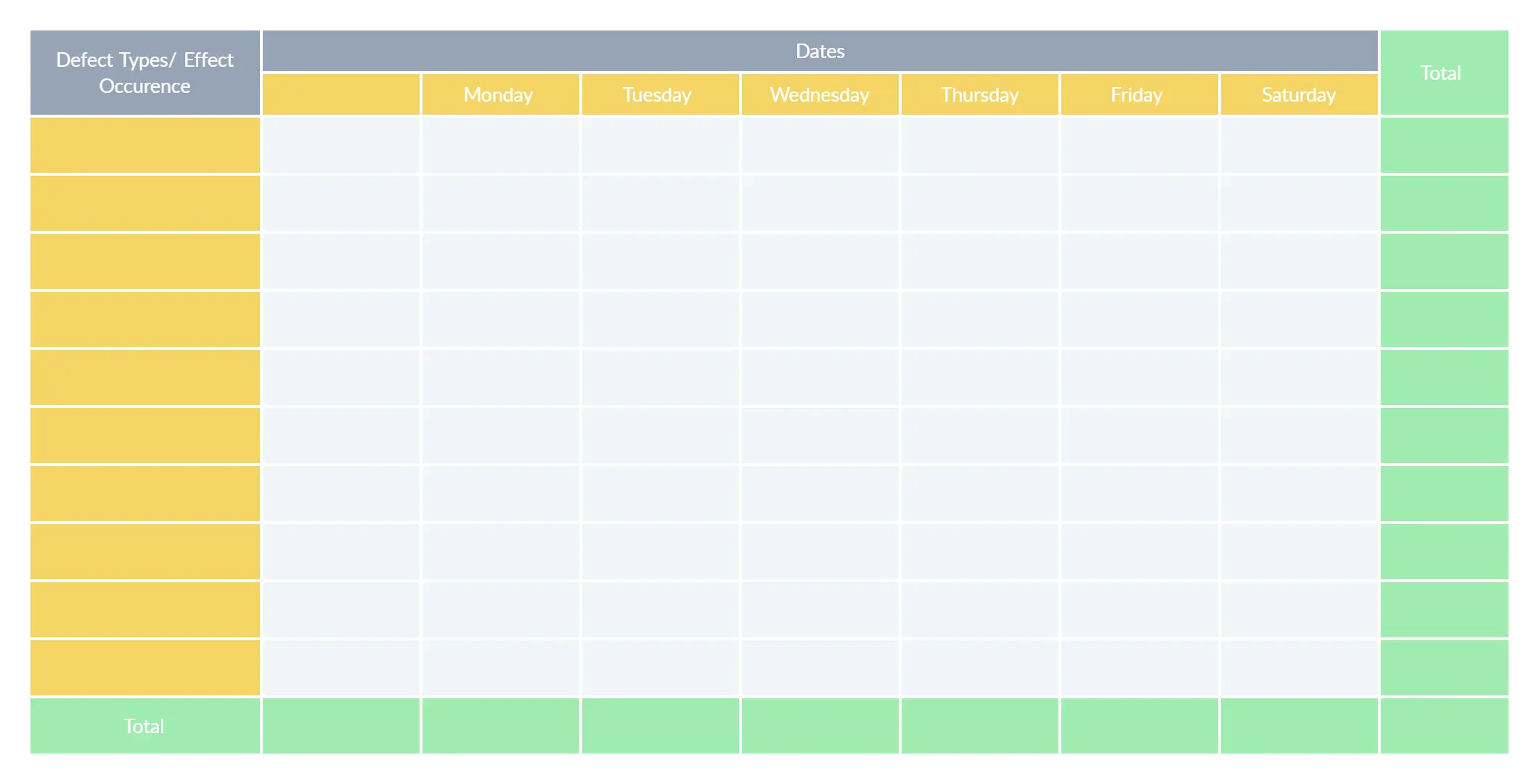
Control Chart
The control chart is a type of run chart used to observe and study process variation resulting from a common or special cause over a period of time.
The chart helps measure the variations and visualize it to show whether the change is within an acceptable limit or not. It helps track metrics such as defects, cost per unit, production time, inventory on hand, etc.
Control charts are generally used in manufacturing, process improvement methodologies like Six Sigma and stock trading algorithms.
Uses
- To determine whether a process is stable.
- To monitor processes and learn how to improve poor performance.
- To recognize abnormal changes in a process.
Real-world examples of usage
- Monitoring the variation in product dimensions during a manufacturing process.
- Tracking the number of customer complaints received per day.
- Monitoring the average response time of a customer support team.
Benefit
Enables real-time monitoring of process stability, early detection of deviations or abnormalities, and prompt corrective actions to maintain consistent quality.
How to create a control chart
- Gather data on the characteristic of interest.
- Calculate mean and upper/lower control limits.
- Create a graph and plot the collected data.
- Add lines representing the mean and control limits to the graph.
- Look for patterns, trends, or points beyond control limits.
- Determine if the process is in control or out of control.
- Investigate and address causes of out-of-control points.
- Regularly update the chart with new data and analyze for ongoing improvement.
Who can use it?
- Production supervisors or operators monitoring process performance on the shop floor.
- Quality control or assurance personnel tracking variation in product quality over time.
- Service managers observing customer satisfaction levels and service performance metrics.
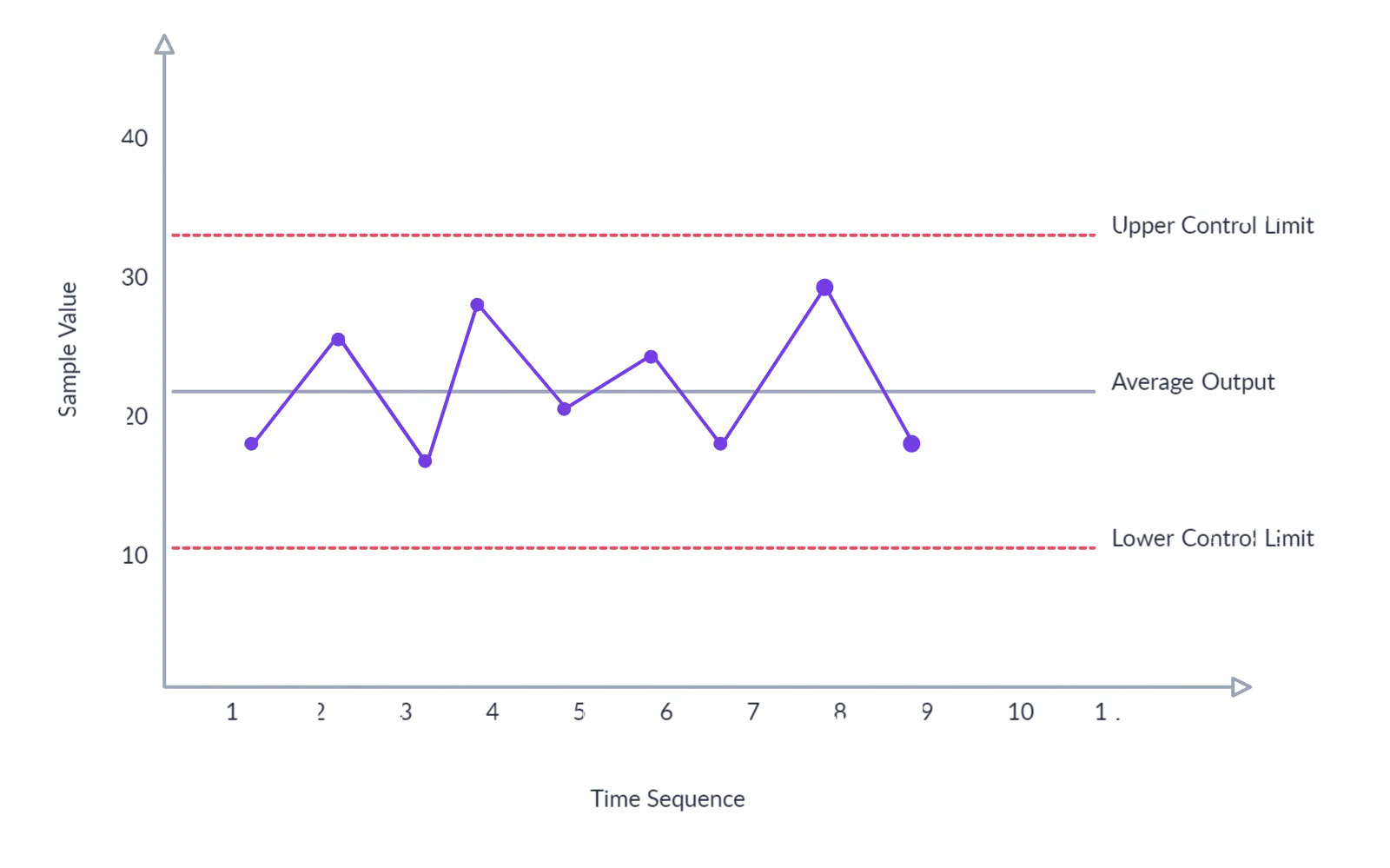
Pareto Chart
The Pareto chart is a combination of a bar graph and a line graph. It helps identify the facts needed to set priorities.
The Pareto chart organizes and presents information in such a way that makes it easier to understand the relative importance of various problems or causes of problems. It comes in the shape of a vertical bar chart and displays the defects in order (from the highest to the lowest) while the line graph shows the cumulative percentage of the defect.
Uses
- To identify the relative importance of the causes of a problem.
- To help teams identify the causes that will have the highest impact when solved.
- To easily calculate the impact of a defect on the production.
Real-world examples of usage
- Analyzing customer feedback to identify the most common product or service issues.
- Prioritizing improvement efforts based on the frequency of quality incidents.
- Identifying the major causes of delays in project management.
Benefit
Helps focus improvement efforts on the most significant factors or problems, leading to effective allocation of resources and improved outcomes.
How to create a Pareto chart
- Select the problem for investigation. Also, select a method and time for collecting information. If necessary create a check sheet for recording information.
- Once you have collected the data, go through them and sort them out to calculate the cumulative percentage.
- Draw the graph, bars, cumulative percentage line and add labels (refer to the example below).
- Analyze the chart to identify the vital few problems from the trivial many by using the 80/20 rule. Plan further actions to eliminate the identified defects by finding their root causes.
Who can use it?
- Quality managers or improvement teams looking to prioritize improvement initiatives.
- Project managers seeking to identify and address the most critical project risks.
- Sales or marketing teams analyzing customer feedback or product issues.

What’s Your Favorite Out of the 7 Basic Quality Tools?
You can use these 7 basic quality tools individually or together to effectively investigate processes and identify areas for improvement. According to Ishikawa, it’s important that all employees learn how to use these tools to ensure the achievement of excellent performance throughout the organization.
Got anything to add to our guide? Let us know in the comments section below.
FAQs about 7 Basic Quality Tools
Quality problems in an organization can manifest in various forms and affect different areas of operations.
- Product defects: Products may have defects or non-conformities that deviate from quality specifications, leading to customer dissatisfaction, returns, or warranty claims.
- Service errors: Service errors can occur when services do not meet customer expectations, such as incorrect billing, delays in delivery, or inadequate customer support.
- Process inefficiencies: Inefficient processes can lead to delays, errors, or rework, resulting in increased costs, decreased productivity, and customer dissatisfaction.
- Poor design or innovation: Inadequate product design or lack of innovation can lead to products that do not meet customer needs, lack competitive features, or have usability issues.
- Supplier quality issues: Poor quality materials or components from suppliers can affect the overall quality of the final product or service.
- Ineffective quality management systems: Inadequate quality management systems, such as lack of quality standards, processes, or documentation, can contribute to quality problems throughout the organization.
The basic quality improvement steps typically follow a systematic approach to identify, analyze, implement, and monitor improvements in processes or products.
- Clearly articulate the problem or identify the area for improvement.
- Collect relevant data and information related to the problem.
- Analyze the collected data to identify patterns, root causes, and opportunities for improvement.
- Brainstorm and generate potential improvement ideas or solutions.
- Assess the feasibility, impact, and effectiveness of the generated improvement ideas.
- Develop an action plan to implement the chosen solution.
- Continuously monitor and measure the results of the implemented solution.
- Based on the monitoring results, evaluate the effectiveness of the implemented solution.
- Once the improvement is successful, document the new processes, best practices, or standard operating procedures (SOPs).
- Iterate through the steps to continuously improve processes and products.