The most commonly used methodology in Six Sigma is the DMAIC process. Many use it to solve problems and identify and fix errors in business and manufacturing processes.
In this post, we will look at how to use the DMAIC process to solve problems. You will also find useful and editable templates that you can use right away when implementing DMAIC problem-solving in your organization.
- What are 5 the Steps of Six Sigma
- DMAIC Process and Problem-Solving
- Common Mistakes to Avoid when Using Six Sigma DMAIC Methodology
- How to Use the DMAIC Methodology for Problem Solving in Project Management
What are the 5 Steps of Six Sigma
DMAIC is one of the core methodologies used within the Six Sigma framework. It is a data-driven method used to systematically improve the process. The approach aims to increase the quality of a product or service by focusing on optimizing the process that produces the output. This way DMAIC seeks to provide permanent solutions when it comes to process improvement.
It provides a structured problem-solving framework to identify, analyze, and improve existing processes. DMAIC guides practitioners through a series of steps to identify the root causes of process issues, implement solutions, and sustain the improvements over time.
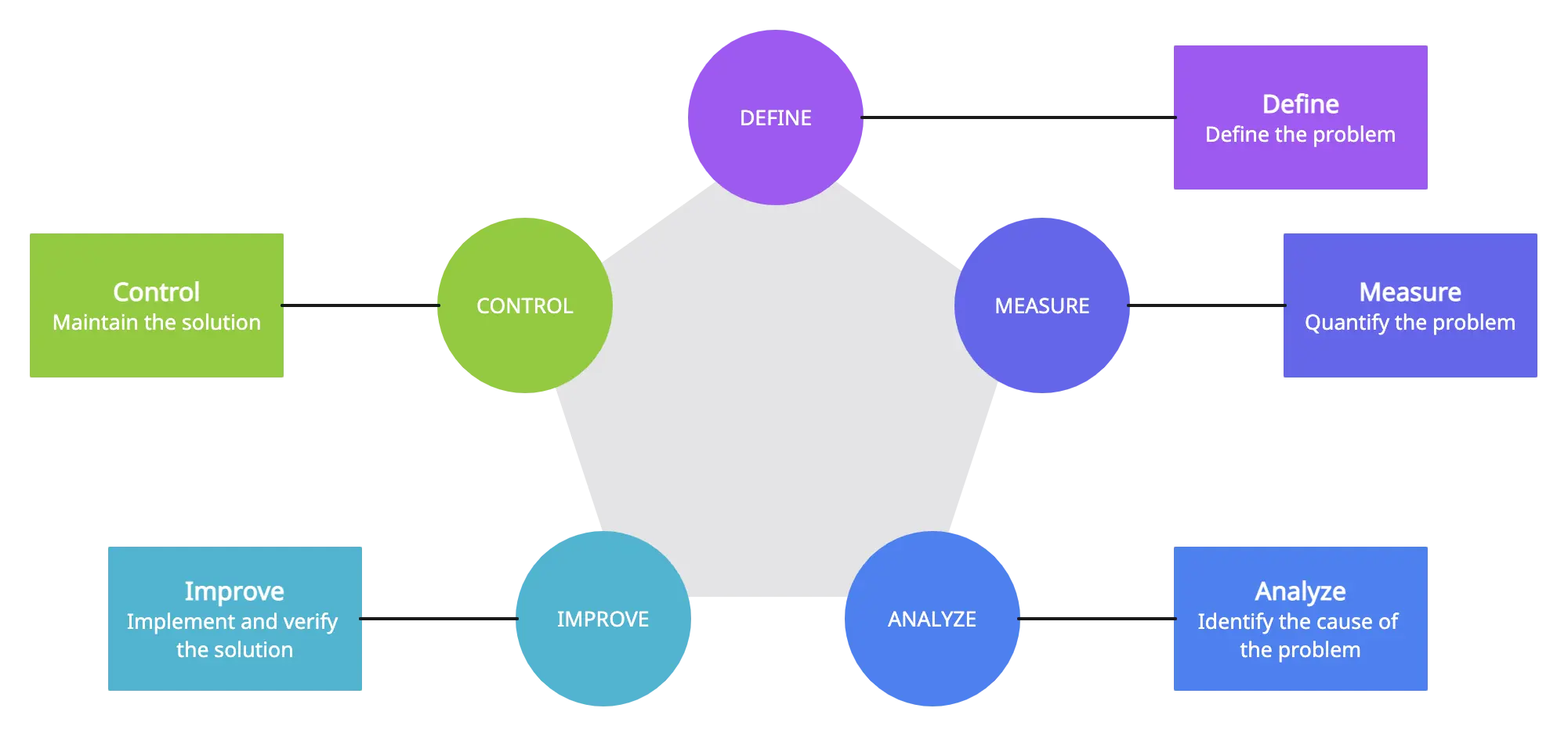
DMAIC Process and Problem-Solving
Following we have listed down the 5 phases of the DMAIC process along with the steps you need to take when using it to solve problems. Different tools for each phase is provided with editable templates.
Step 1: Define the Problem
So there’s a problem that affects your customer or your company processes. In this first step of the DMAIC problem solving method, you need to focus on what the problem is and how it has affected you as a company.
There are a few steps you need to follow in this phase.
• Create a problem statement which should include a definition of the problem in quantifiable terms and the severity of the problem.
• Make sure necessary resources such as a team leader and competent team members, and funds etc. are available at hand.
• Develop a goal statement based on your problem statement. It should be a measurable and time-bound target to achieve.
• Create a SIPOC diagram which will provide the team with a high-level overview of the process (along with its inputs, outputs, suppliers, and customers) that is being analyzed. You can also use a value stream map to do the same job.
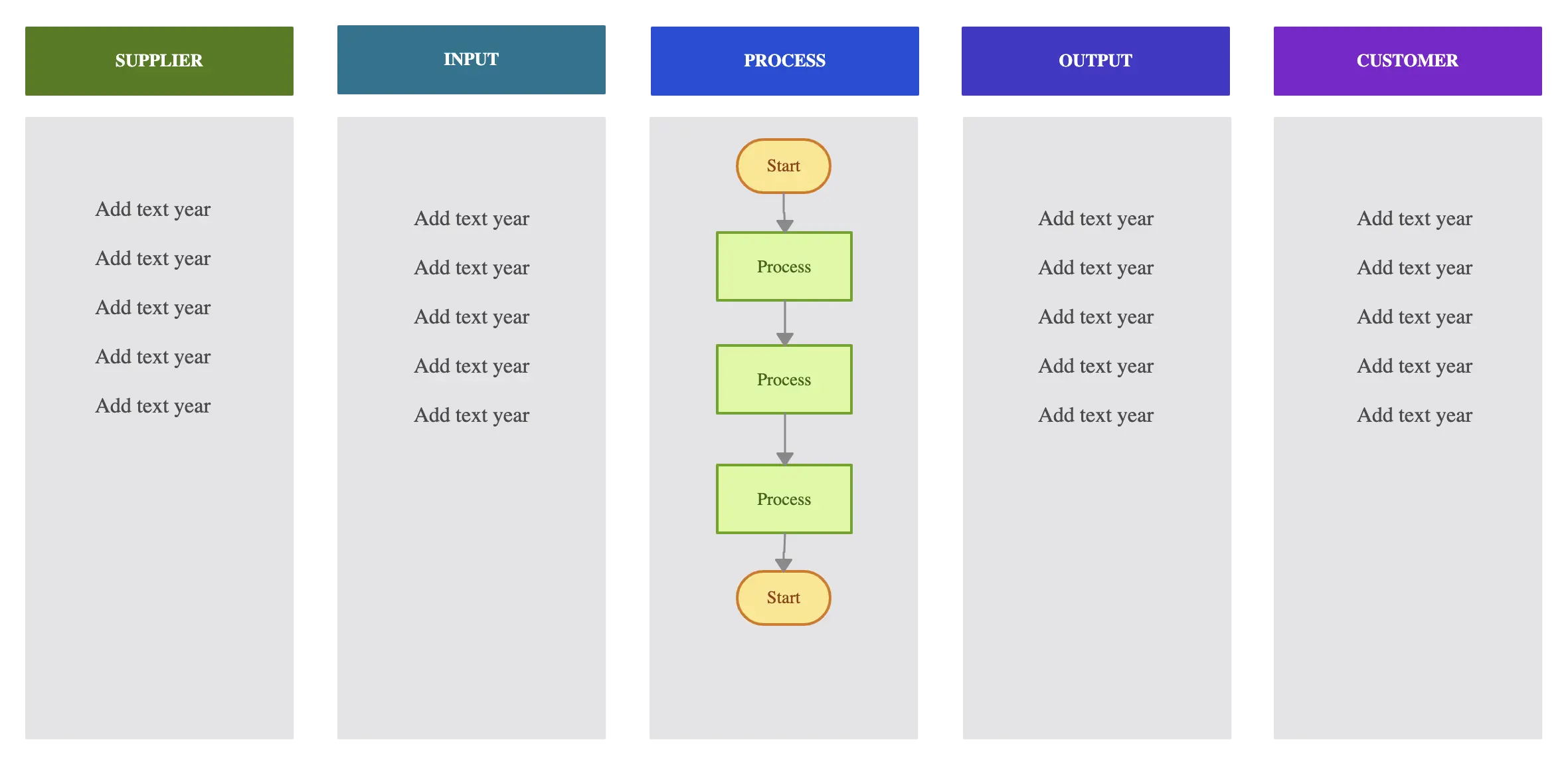
• Try to understand the process in more in-depth detail by creating a process map that outlines all process steps. Involve the process owners when identifying the process steps and developing the map. You can add swimlanes to represent different departments and actors responsible.
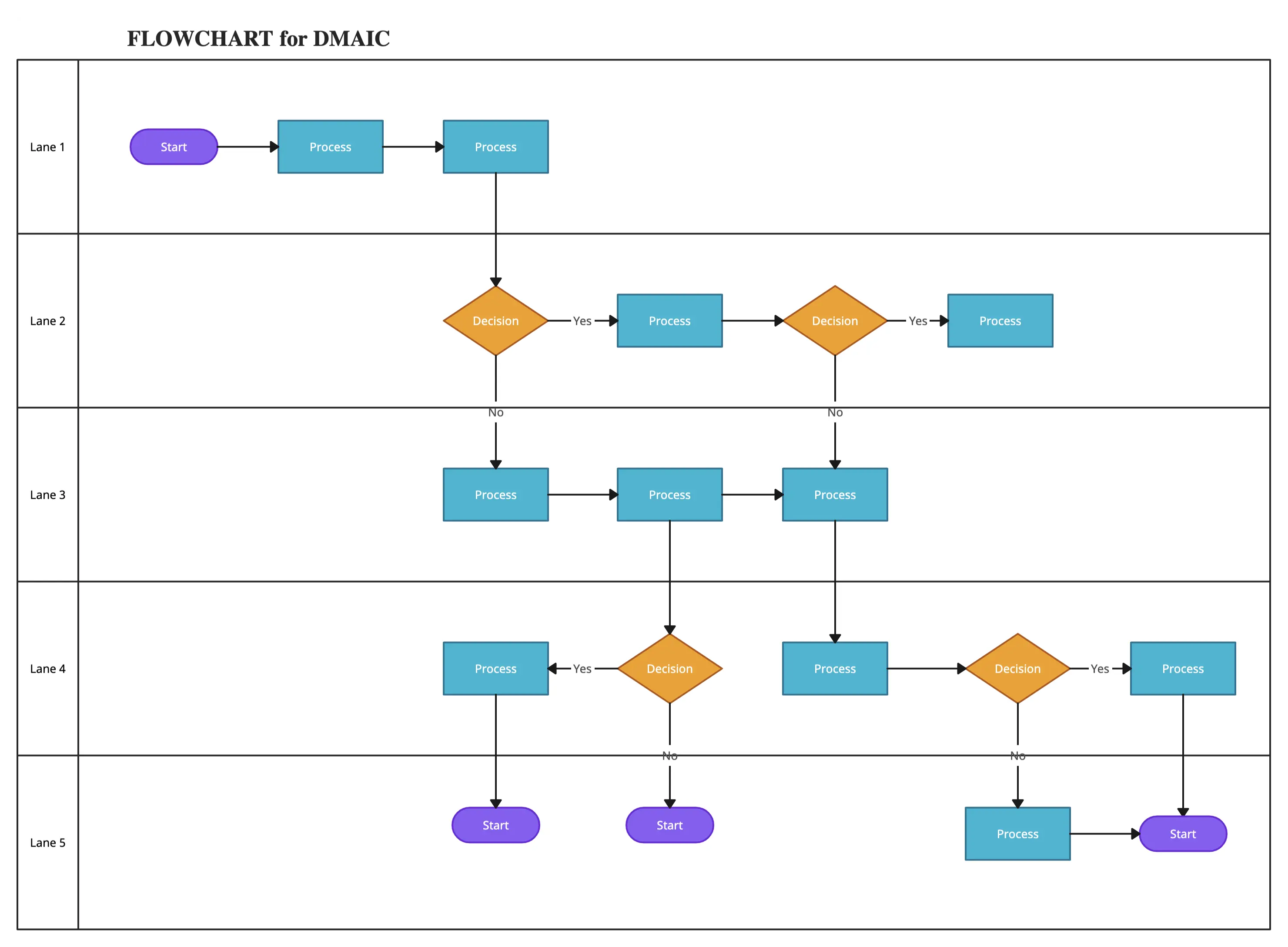
Step 2: Measure the Problem
In this step, you should measure the extent of the problem. To do so you need to examine the process in its current state to see how it performs. The detailed process map you created in the ‘Define’ phase can help you with this.
The baseline measurements you will need to look into in this phase, are process duration, the number of defects, costs and other relevant metrics.
These baseline measurements will be used as the standards against which the team will measure their success in the ‘Improve’ phase.
Step 3: Analyze the Problem
The analyze phase of the DMAIC process is about identifying the root cause that is causing the problem.
• Referring to the process maps and value stream maps you have created, further, analyze the process to identify the problem areas.
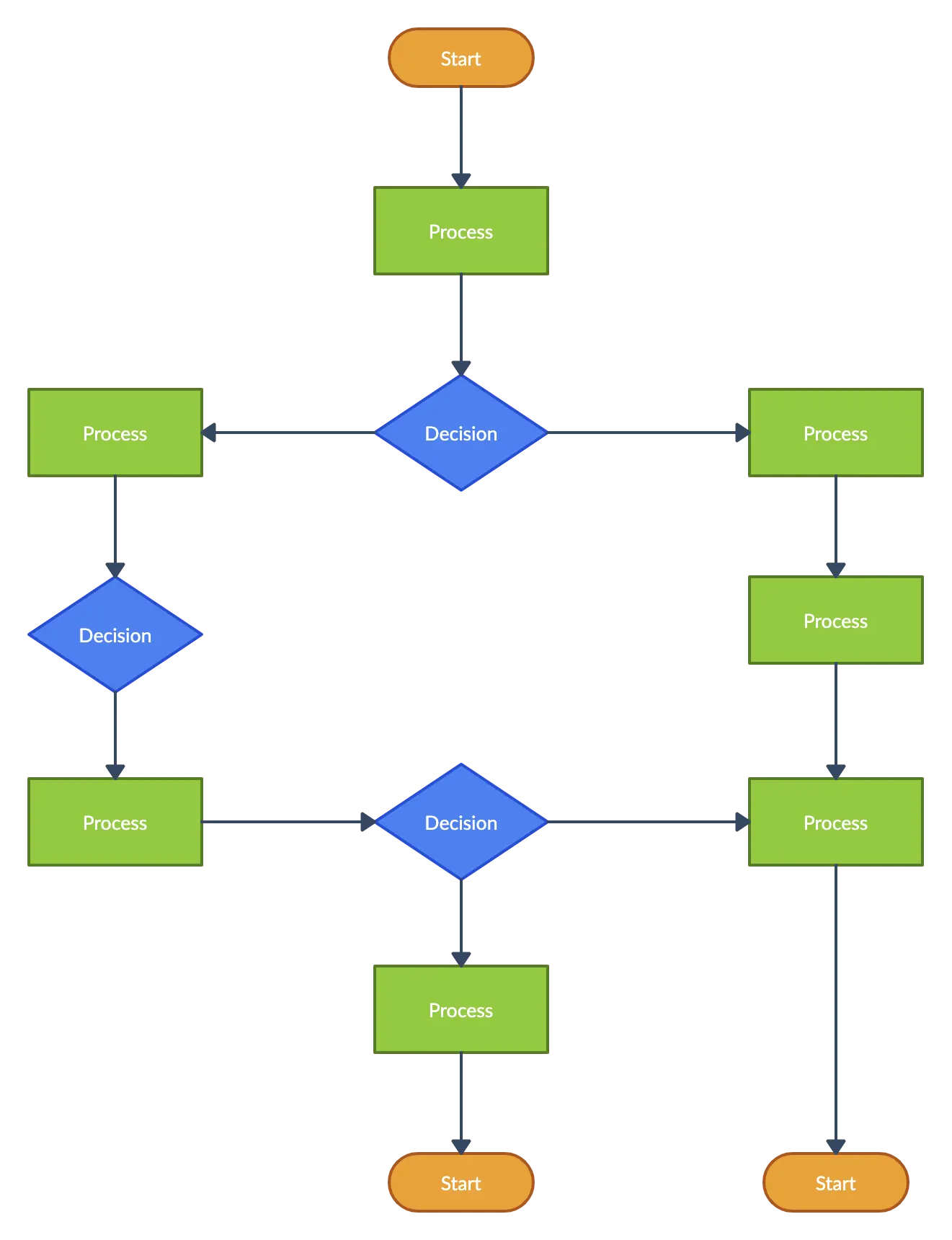
• Visualize the data you have collected (both in the ‘Measure’ phase and the analyze phase) to identify signs of problems in the processes.
• Use Pareto charts, histograms, run charts etc. to represent numerical data. Study them with team leaders and process owners to identify patterns.
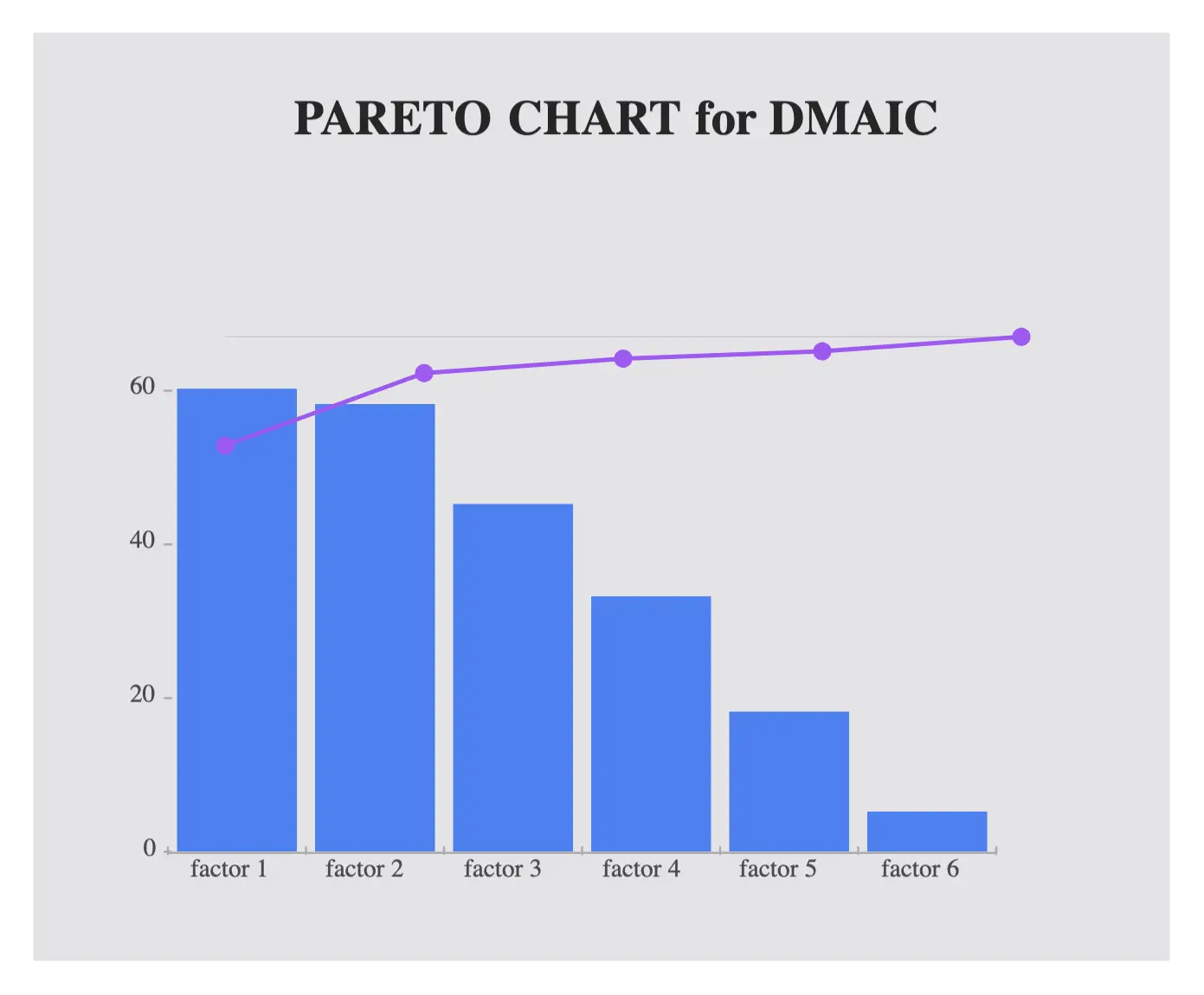
• With the results of your process analysis and your data analysis, start brainstorming the root causes of the problem. Use a cause and effect diagram/ fishbone diagram to capture the knowledge of the process participants during the session.
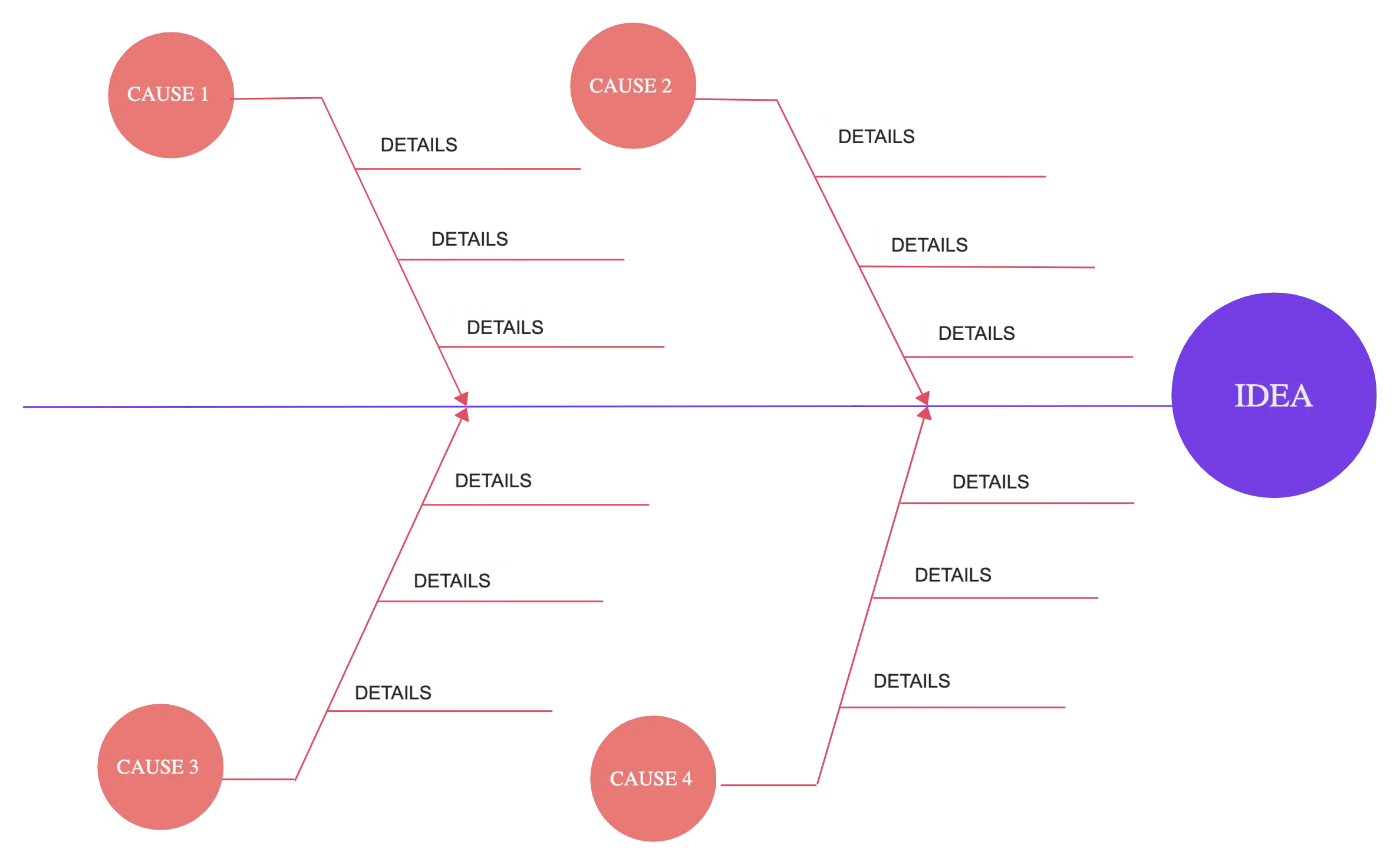
• Using a 5 whys diagram, narrow down your findings to the last few causes of the problem in your process.
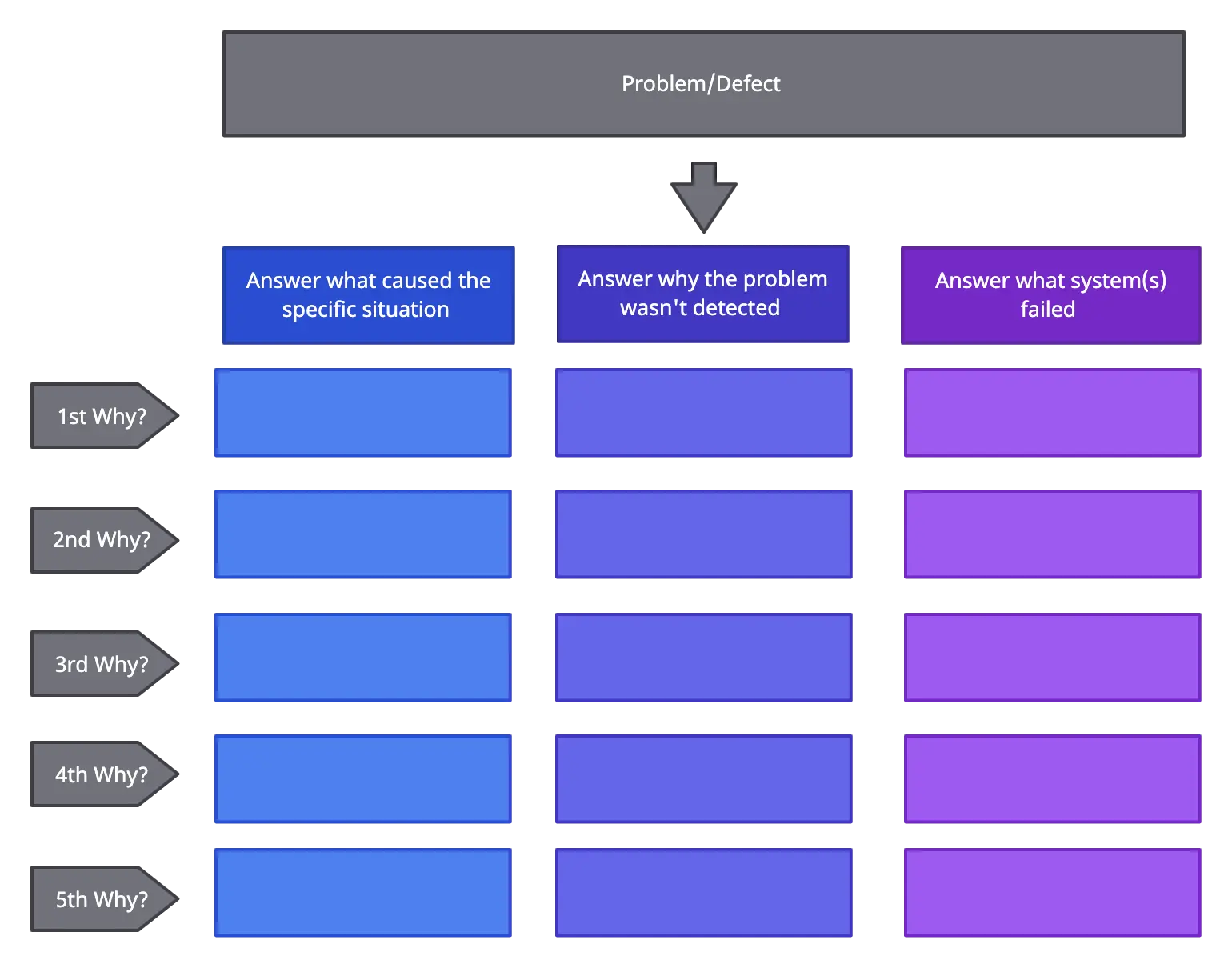
Step 4: Improve (Solve the Problem)
In this phase, the focus is on mitigating the root cause identified and brainstorming and implementing solutions. The team will also collect data to measure their improvement against the data collected during the ‘Measure’ phase.
• You may generate several effective solutions to the root cause, but implementing them all would not be practical. Therefore, you will have to select the most practical solutions.
To do this you can use an impact effort matrix. It will help you determine which solution has the best impact and the least effort/ cost.
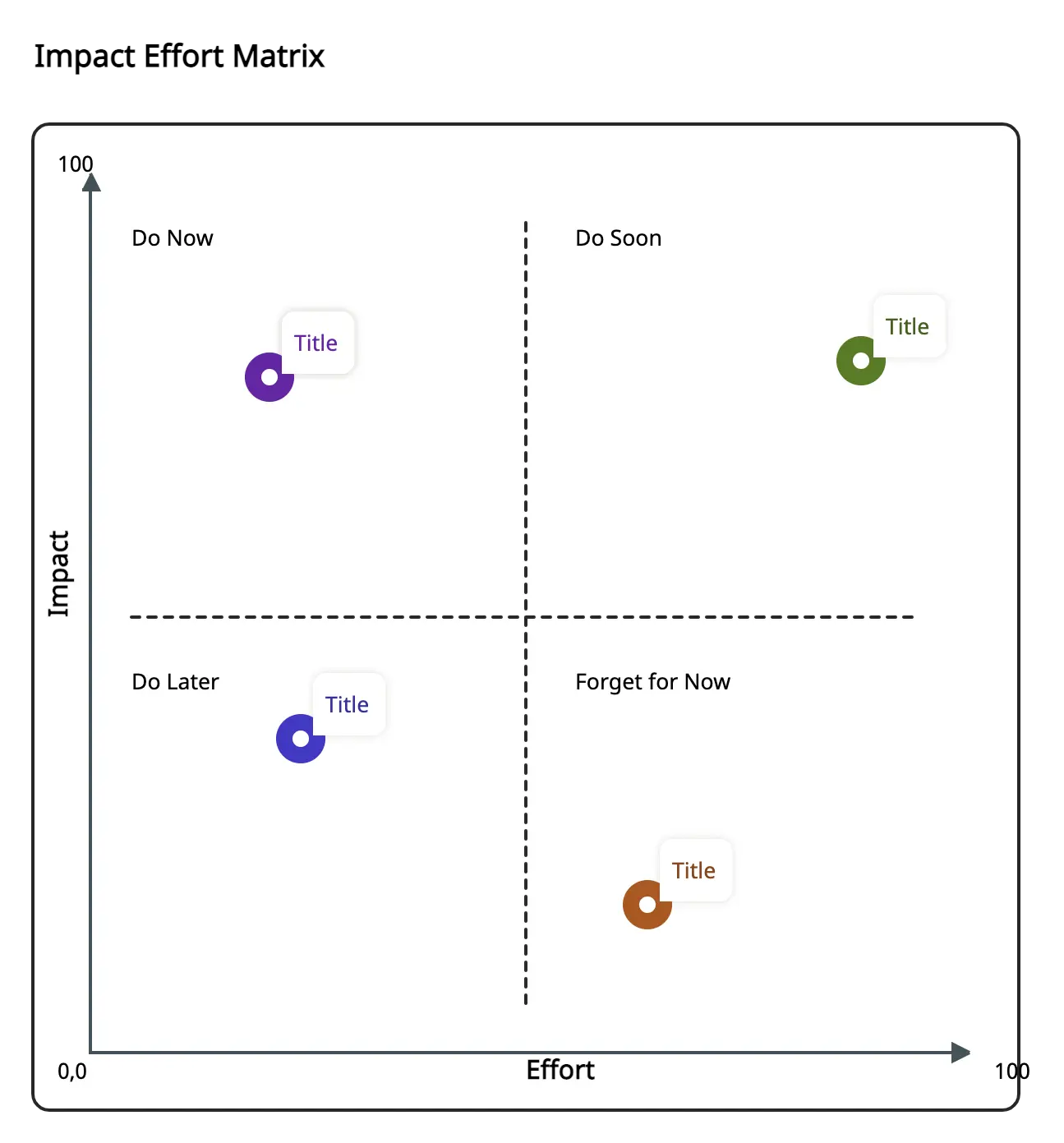
• Based on different solutions, you should develop new maps that will reflect the status of the process once the solution has been applied. This map is known as the to-be map or the future-state map. It will provide guidance for the team as they implement changes.
• Explore the different solutions using the PDCA cycle and select the best one to implement. The cycle allows you to systematically study the possible solutions, evaluate the results and select the ones that have a higher chance of success.
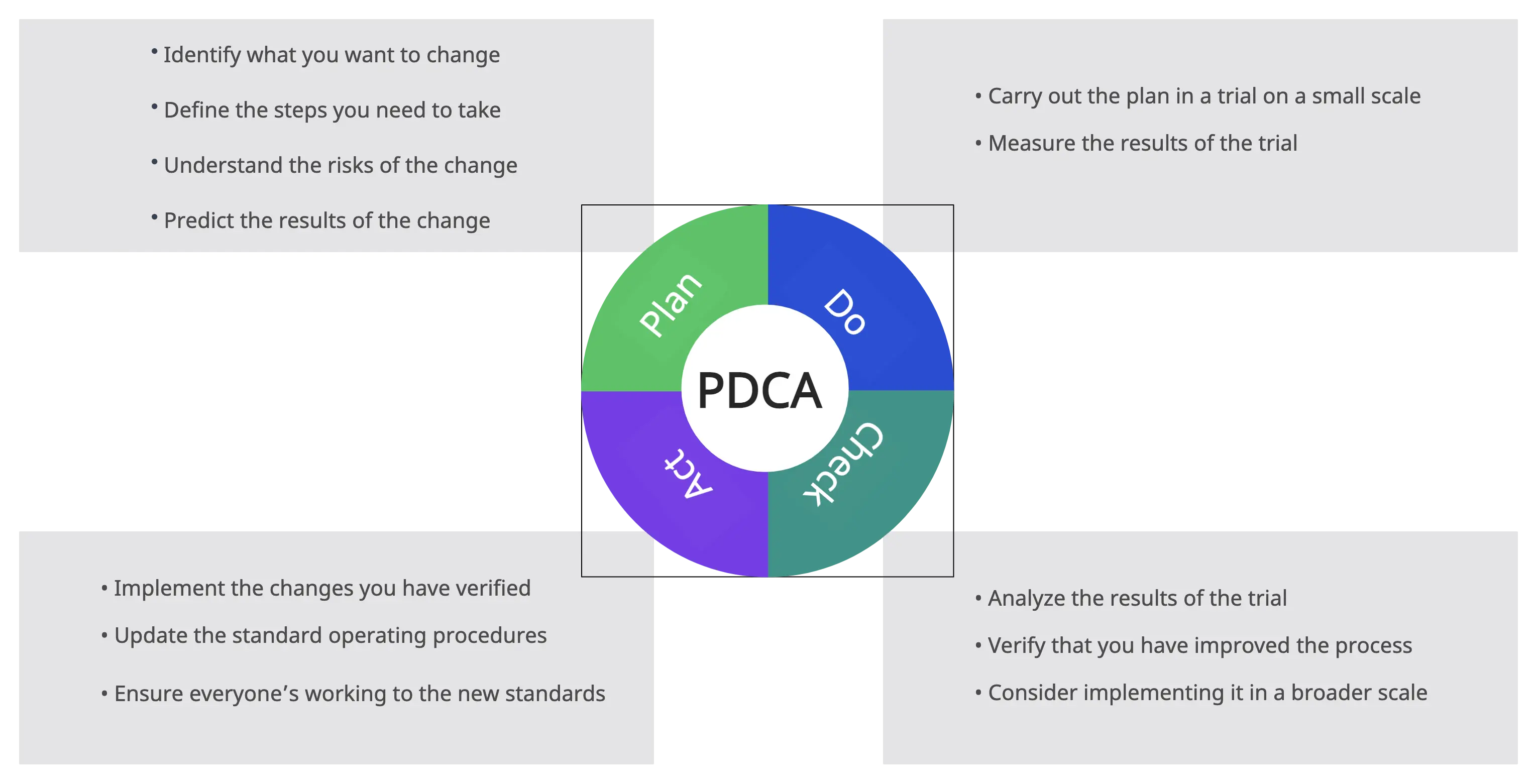
Step 5: Control (Sustain the Improvements)
In the final phase of the DMAIC method , the focus falls on maintaining the improvements you have gained by implementing the solutions. Here you should continue to measure the success and create a plan to monitor the improvements (a Monitoring plan).
You should also create a Response plan which includes steps to take if there’s a drop in the process performance. With new process maps and other documentation, you should then proceed to document the improved processes.
Hand these documents along with the Monitoring plan and the response plan to the process owners for their reference.
Common Mistakes to Avoid when Using Six Sigma DMAIC Methodology
Insufficiently defining the problem can lead to a lack of clarity regarding the problem statement, objectives, and scope. Take the time to clearly define the problem, understand the desired outcomes, and align stakeholders' expectations.
Failing to engage key stakeholders throughout the DMAIC process can result in limited buy-in and resistance to change. Ensure that stakeholders are involved from the beginning, seeking their input, addressing concerns, and keeping them informed about progress and outcomes.
Collecting insufficient or inaccurate data can lead to flawed analysis and incorrect conclusions. Take the time to gather relevant data using appropriate measurement systems, ensure data accuracy and reliability, and apply appropriate statistical analysis techniques to derive meaningful insights.
Getting caught up in analysis paralysis without taking action is a common pitfall. While analysis is crucial, it’s equally important to translate insights into concrete improvement actions. Strive for a balance between analysis and implementation to drive real change.
Failing to test potential solutions before implementation can lead to unintended consequences. Utilize methods such as pilot studies, simulation, or small-scale experiments to validate and refine proposed solutions before full-scale implementation.
Successful process improvement is not just about making initial changes; it’s about sustaining those improvements over the long term. Develop robust control plans, standard operating procedures, and monitoring mechanisms to ensure the gains achieved are maintained and deviations are identified and corrected.
Applying DMAIC in a one-size-fits-all manner without considering the organization’s unique culture, context, and capabilities can hinder success. Tailor the approach to fit the specific needs, capabilities, and culture of the organization to enhance acceptance and implementation.
How to Use the DMAIC Methodology for Problem Solving in Project Management
Define
In the project management context, the Define phase involves clearly defining the project objectives, scope, deliverables, and success criteria. It entails identifying project stakeholders, understanding their expectations, and establishing a project charter or a similar document that outlines the project’s purpose and key parameters.
Measure
The Measure phase focuses on collecting data and metrics to assess the project’s progress, performance, and adherence to schedule and budget. Key project metrics such as schedule variance, cost variance, and resource utilization are tracked and analyzed. This phase provides insights into the project’s current state and helps identify areas that require improvement.
Analyze
The Analyze phase involves analyzing the project data and identifying root causes of any performance gaps or issues. It aims to understand why certain project aspects are not meeting expectations. Techniques such as root cause analysis, Pareto charts, or fishbone diagrams can be used to identify factors impacting project performance.
Improve
In the Improve phase, potential solutions and actions are developed and implemented to address the identified issues. This may involve making adjustments to the project plan, reallocating resources, refining processes, or implementing corrective measures. The goal is to optimize project performance and achieve desired outcomes.
Control
The Control phase focuses on monitoring and controlling project activities to sustain the improvements made. It involves implementing project control mechanisms, establishing performance metrics, and conducting regular reviews to ensure that the project remains on track. Control measures help prevent deviations from the plan and enable timely corrective actions.
What are Your Thoughts on DMAIC Problem Solving Method?
Here we have covered the 5 phases of Six Sigma DMAIC and the tools that you can use in each stage. You can use them to identify problem areas in your organizational processes, generate practical solutions and implement them effectively.
Have you used DMAIC process to improve processes and solve problems in your organization? Share your experience with the tool with us in the comment section below.
Also, check our post on Process Improvement Methodologies to learn about more Six Sigma and Lean tools to streamline your processes.
FAQs about Six Sigma and DMAIC Approaches
DMAIC and DMADV are two methodologies used in Six Sigma. DMAIC is employed to enhance existing processes by addressing issues and improving efficiency, while DMADV is utilized for creating new processes or products that meet specific customer needs by following a structured design and verification process.
DMAIC:
- Used for improving existing processes
- Define, Measure, Analyze, Improve, Control
- Identifies problem areas and implements solutions
- Focuses on reducing process variation and enhancing efficiency
DMADV:
- Used for developing new products, services, or processes
- Define, Measure, Analyze, Design, Verify
- Emphasizes meeting customer requirements and creating innovative solutions
- Involves detailed design and verification through testing
Problem identification: When a process is not meeting desired outcomes or experiencing defects, DMAIC can be used to identify and address the root causes of the problem.
Process optimization: DMAIC provides a systematic approach to analyze and make improvements to processes by reducing waste, improving cycle time, or enhancing overall efficiency.
Continuous improvement: DMAIC is often used as part of ongoing quality management efforts. It helps organizations maintain a culture of continuous improvement by systematically identifying and addressing process issues, reducing variation, and striving for better performance.
Data-driven decision making: DMAIC relies on data collection, measurement, and analysis. It is suitable when there is sufficient data available to evaluate process performance and identify areas for improvement.
Quality control and defect reduction: DMAIC is particularly useful when the primary objective is to reduce defects, minimize errors, and enhance product or service quality. By analyzing the root causes of defects, improvements can be made to prevent their occurrence.